From manual to intelligent: the development history of drilling buttons
The progress of the industry is inseparable from the innovation of every subtle component. As a key element of the mechanical equipment, the drilling button has undergone many technological upgrades. The original manual mechanical version required the operator to participate in the control of the whole process, which was time-consuming and labor-intensive. With the development of science and technology, it has now entered the era of intelligence. Modern drilling buttons can not only automatically complete complex task processes, but also monitor the operating status in real time through built-in sensors, which greatly improves the accuracy and safety of production.
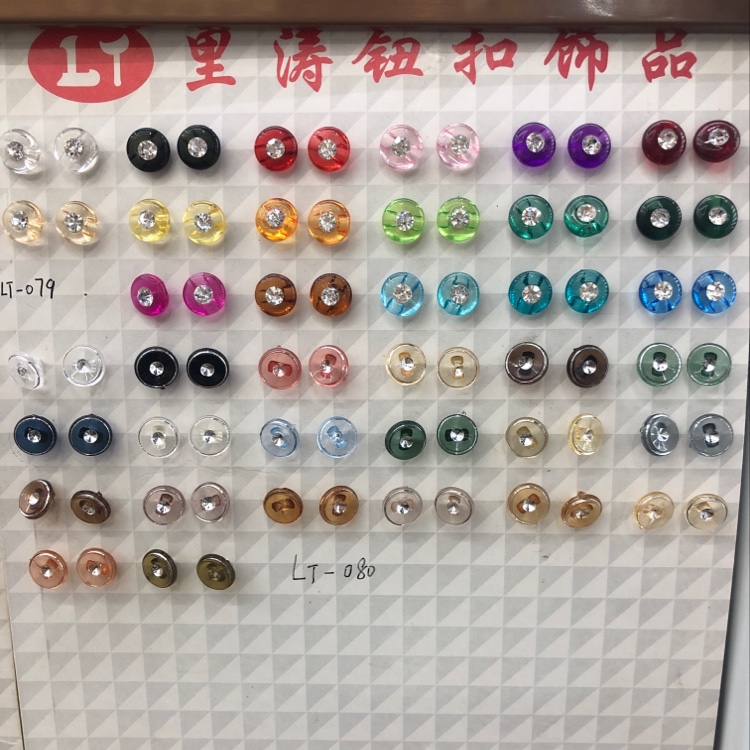
The core of precise control: analysis of the working principle of the drilling button
To gain insight into why this small, compact component is so important, we need to understand how it works. A typical drilling button consists of a trigger device, a signal transmission system, and an actuator. When the button is pressed, the electrical signal is quickly transmitted to the main control unit, and then the motor is activated to drive the drill. Not only that, the advanced model also integrates feedback loops to ensure that each job is under the optimal parameter settings, thereby achieving an unprecedented degree of precision.
Quality is everything: the importance of reliable materials
Choosing the right material is essential to ensure the quality of the drill button. At present, the common materials on the market include high-strength metal alloys and high-performance engineering plastics. The former is known for its excellent wear resistance and stability, which still performs well in harsh environments, while the latter is favored for its lighter weight and excellent electrical insulation properties. Regardless of the material selected, the ultimate goal is to extend service life and maintain stable performance.

Meeting Diverse Needs: Customized Solutions in Different Industries
Various industries have different challenges for drilling buttons due to their special process requirements. In the aerospace sector, for example, special attention is paid to sealing and corrosion protection due to frequent extreme temperature changes; in medical devices, absolute cleanliness standards under sterile conditions are emphasized. Manufacturers have developed a variety of proprietary technologies and improvements to address these issues to cater to the unique needs of each type of customer.
Future trend outlook: the possibility of a new generation of drilling buttons
At the forefront of the digital transformation wave, we can boldly imagine the possibilities of the future. With the support of Internet of Things technology, the new drill button may have a networking function to allow engineers to remotely access equipment data to quickly diagnose the cause of failure and implement preventive maintenance plans. In addition, artificial intelligence algorithms may also be added to enable machines to learn themselves and continuously optimize their operational efficiency to bring more surprise changes to the global manufacturing industry.
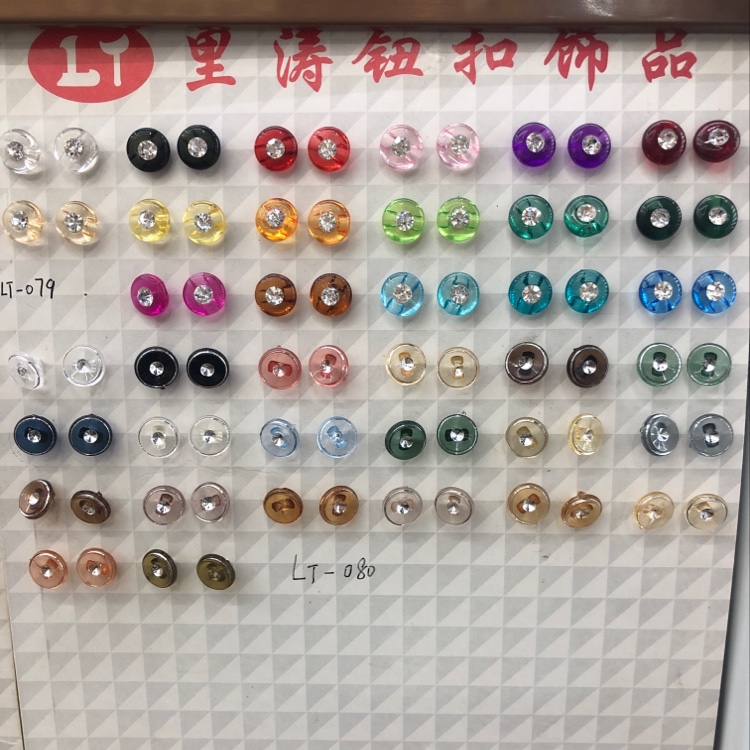