In modern industrial production, each small part has the potential to have a profound impact on overall efficiency. Among them, the drilling button, as a seemingly simple but critical gadget, is gradually becoming one of the core elements in the field of machining and automation control.
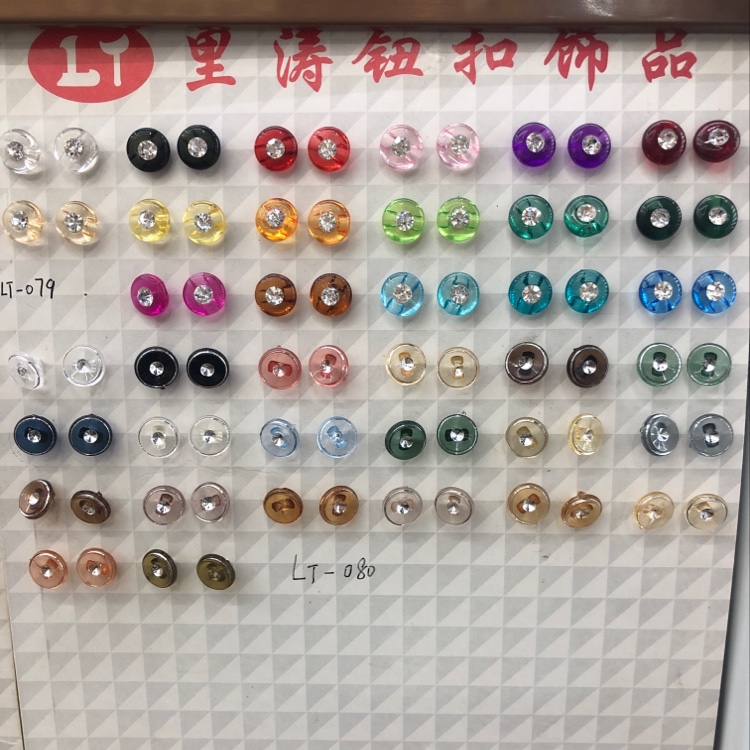
The drilling button is a device specially used to start or stop the operation of mechanical equipment. It is usually designed to be easy to touch and respond quickly. It not only simplifies complex processes, but also significantly reduces the risk of human error, thereby improving the stability and reliability of the entire system. In addition, due to its compact structure and convenient installation, it has shown extremely high adaptability in various manufacturing environments.
For professionals who need precise control, it is especially important to understand the different types and technical specifications. At present, the common drilling buttons on the market are mainly divided into two categories: manual trigger type and electronic sensor type. The former realizes signal transmission through physical contact, while the latter uses advanced sensor technology to capture subtle movements. Regardless of the form, you need to focus on the following aspects:
First is the material selection. The metal shell with strong corrosion resistance is more suitable for long-term use in harsh environments. The second is the sensitivity adjustment range, which directly affects the work efficiency and the error rate. Finally, whether the design of the connection mode is scientific and reasonable, and whether it can support special requirements such as quick disassembly and replacement.
Of course, it is not enough to know this theoretical knowledge, and how to make optimal decisions based on the actual situation is the key to success. For example, in the automobile manufacturing industry, every step on the assembly line must be carried out in strict accordance with the established procedures, so it is more appropriate to choose traditional keys with higher stability. In some high-tech laboratories, non-contact inductive switches are more likely to be used to ensure that the experimental data is absolutely pure and undisturbed.

In addition to the correct selection, good maintenance habits can not be ignored. Regular cleaning of surface dust and stains can not only extend the service life, but also ensure that you can get an immediate response after each press. At the same time, it is recommended to recalibrate the set value at regular intervals to avoid drift caused by long-term operation.
All in all, there is a huge potential behind the little drill button waiting to be tapped. As long as it is good at discovering and using it flexibly, it can create greater value for the enterprise!
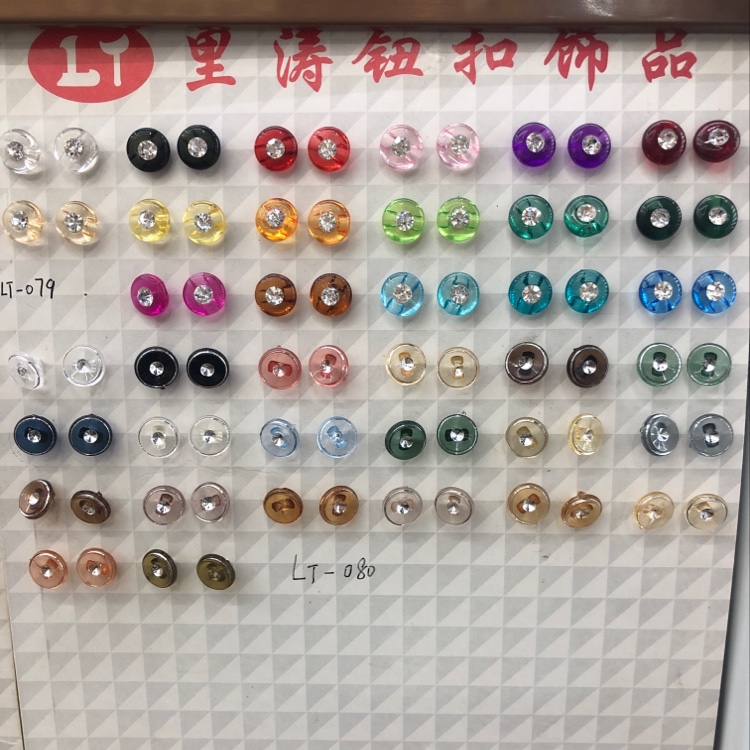